Thursday 16th May 2024
Filtration plays a crucial role in industrial processes by ensuring the purity and quality of products and maintaining the efficiency and reliability of equipment. In various industries such as manufacturing, pharmaceuticals, food, and automotive, filtration is essential for removing contaminants and impurities from fluids and gases.
Vacuum compressor filters are a critical component of filtration systems. These filters are designed to remove contaminants and debris from compressed air to ensure air is clean and free from harmful particles. Understanding how vacuum compressor filters work and their role in filtration systems is important to ensure optimal equipment performance, productivity, and efficiency.
In this blog, we look at the fundamentals of vacuum compressor filters, their benefits in improving efficiency, and the factors influencing their effectiveness in industrial applications.
Vacuum compressor filters are specialised filtration devices designed to remove contaminants, impurities, and particles from compressed air and gas. These filters ensure that the air supplied to machinery and equipment is clean to maintain product quality and equipment efficiency.
Vacuum compressor filters can remove solid particles, moisture, oil mist, and other liquid contaminants. This helps prevent corrosion and guarantees consistent performance in workshops and factories.
Vacuum Compressors generate compressed air which has become an essential energy source in modern manufacturing. Due to the extreme loads mobile & Stationary compressors are under, effective protection of components is essential.
Filtration Ltd can offer a range of filters in various sizes, configurations, and ratings to suit a variety of applications and operating conditions to ensure your machinery operates reliably.
There are many ways in how vacuum filters improve efficiency such as preventing damage, maintaining product quality, minimising maintenance requirements, and reducing energy consumption.
By capturing dust, dirt, and moisture, among other contaminants, air compressor filters prevent these particles from entering sensitive equipment components. This reduces the risk of damage and corrosion and, consequently, prolongs the lifespan of machinery.
The process of collecting contaminants also enables optimal operating conditions for mobile & stationary compressors, even in challenging conditions. In turn, this reduces energy consumption and the associated costs by preventing inefficiencies in the filtration process. This is especially important for industries and organisations looking to reduce their overall energy emissions.
In addition, regularly replacing the filter can further improve efficiency. Replacing the filter at regular intervals prevents damage and clogging. When filters become clogged, the system and machinery must work harder. By ensuring filters are changed before they exceed capacity, the associated workload is reduced, and less energy is required to operate equipment.
Furthermore, the clean air supplied by vacuum compressor filters ensures consistent performance and operation, consequently reducing downtime and the risk of disruption. This helps maintain product quality and prevents contamination.
Vacuum compressor filters have several applications across various industries, where the cleanliness and purity of compressed air and gas are essential to business operations.
By filtering out impurities and contaminants, air filters are used to ensure product quality and integrity in manufacturing. Vacuum compressor filters purify the air in machinery and product lines to prevent defects and maintain a consistent standard.
In the food and beverage industry, vacuum filters and the filtration process are often used to separate particulates from beverages and extract compounds from food samples. This plays a crucial role in allowing food and beverage production companies to maintain hygiene and safety standards. Typically, air filters are also used to control and remove contaminants from compressed air used in food processing, packaging, and storage.
In pharmaceuticals, vacuum compressor filters are essential to pharmaceutical manufacturing processes. They help to efficiently separate and collect solid compounds from a sample mixture. This method ensures the purity and quality of the final compound.
Air filters are used in various automotive industry applications, including paint booths, assembly lines, and tools. By utilising vacuum compressor filters, automotive businesses can rely on quality paintwork and finishes, production efficiency, and high performance.
There are also several different types of vacuum compressor filters. To determine which vacuum filter you need, consider the operating conditions, identify the contaminants, and evaluate the installation requirements.
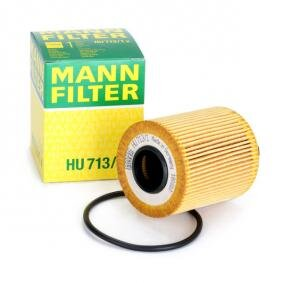
Oil filters are indispensable components in vacuum compressor systems, providing essential protection against contaminants that could jeopardise the efficiency and longevity of the equipment. They excel in capturing particles of various sizes suspended in the lubricating oil. This includes contaminants like dust, dirt, metal particles, and other debris that can accumulate during operation. By efficiently trapping these particles, oil filters prevent them from circulating through the compressor system and causing damage to critical components.
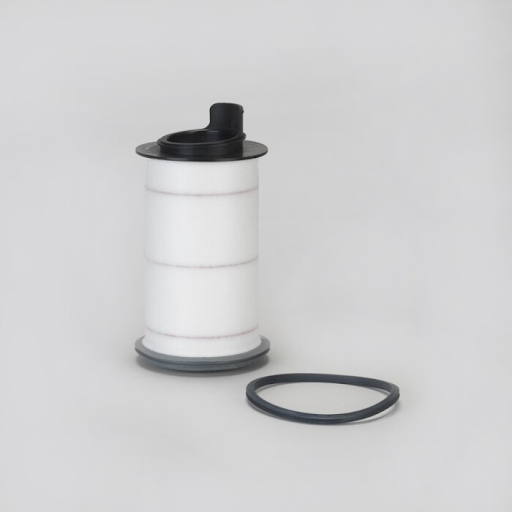
Air/oil separators are critical for maintaining the purity of compressed air and preventing oil contamination in vacuum compressor systems. They are designed to capture oil droplets from the air stream as it passes through. Coalescing filters use fine fibres to trap oil droplets, while centrifugal elements utilise centrifugal force to separate oil from the air. Their efficient oil separation capability helps to prolong the life of downstream equipment and ensures reliable operation of the entire system.
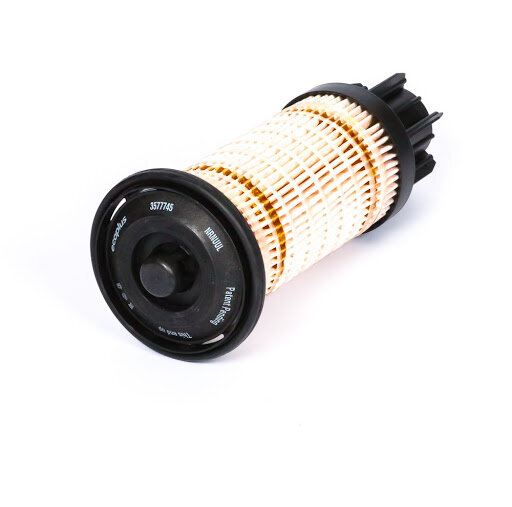
Fuel filters are designed to remove contaminants present in the fuel supply, including dirt, rust, debris, and other particulate matter. These contaminants can enter the fuel system during storage, transportation, or handling, posing a risk of clogging fuel lines, injectors, and other critical components. By effectively trapping contaminants, fuel filters prevent them from reaching sensitive parts of the compressor system, ensuring uninterrupted operation and preventing potential damage.
Several factors can influence the efficiency of vacuum compressor filters. Understanding these factors can help you choose the right filter and optimise filter performance to improve efficiency.
The nature and size of contaminants can significantly impact filter performance and efficiency. Filters are designed to capture specific types of particles. Therefore, it is crucial to match the filter type to the contaminant.
The material of the filtration media determines the filter's efficiency. Different filtration media have varying pore sizes and surface properties that impact their ability to capture contaminants. Refer to the manufacturer recommendations for suitable filtration media.
High airflow rates can reduce efficiency during the filtration process if the filter media cannot capture contaminants at high velocity. Therefore, it is essential to choose a vacuum filter that can maintain high efficiency at the required airflow rate.
Proper installation and sealing are essential to maximising efficiency. Poorly installed filters or leaks in the system can allow contaminants to bypass the filter. Always ensure the seal is tight to ensure efficient filtration.
For maximum efficiency, regular maintenance, such as inspection, cleaning, and filter replacement, is required. If a filter is clogged, it can cause pressure to drop, reducing airflow and efficiency.
We provide Vacuum Compressor filters designed to deliver superior performance and reliability in demanding environments. Whether it's air, oil, or fuel filtration, we can provide parts that effectively remove contaminants while maintaining optimal flow rates and pressure levels. This ensures the continued efficiency and longevity of vacuum compressor systems, even under tough operating conditions.
At Filtration, we are experts in filtration technology and a leading supplier of quality filtration products to a wide range of industries across the UK. We provide a variety of vacuum compressor filters, alongside additional services such as cataloguing, consignment stock, bespoke labelling, oil analysis, and LEV testing.
No matter what you need, Filtration has the solution to meet your filtration needs and will support you every step of the way.
Get in touch today to discover how we can help improve your filtration processes and keep your operations running smoothly.
Vacuum compressor filters are a critical component of filtration systems. These filters are designed to remove contaminants and debris from compressed air to ensure air is clean and free from harmful particles. Understanding how vacuum compressor filters work and their role in filtration systems is important to ensure optimal equipment performance, productivity, and efficiency.
In this blog, we look at the fundamentals of vacuum compressor filters, their benefits in improving efficiency, and the factors influencing their effectiveness in industrial applications.
Fundamentals of Vacuum Compressor Filters
Vacuum compressor filters are specialised filtration devices designed to remove contaminants, impurities, and particles from compressed air and gas. These filters ensure that the air supplied to machinery and equipment is clean to maintain product quality and equipment efficiency.
Vacuum compressor filters can remove solid particles, moisture, oil mist, and other liquid contaminants. This helps prevent corrosion and guarantees consistent performance in workshops and factories.
Vacuum Compressors generate compressed air which has become an essential energy source in modern manufacturing. Due to the extreme loads mobile & Stationary compressors are under, effective protection of components is essential.
Filtration Ltd can offer a range of filters in various sizes, configurations, and ratings to suit a variety of applications and operating conditions to ensure your machinery operates reliably.
How Vacuum Compressor Filters Improve Efficiency
There are many ways in how vacuum filters improve efficiency such as preventing damage, maintaining product quality, minimising maintenance requirements, and reducing energy consumption.
By capturing dust, dirt, and moisture, among other contaminants, air compressor filters prevent these particles from entering sensitive equipment components. This reduces the risk of damage and corrosion and, consequently, prolongs the lifespan of machinery.
The process of collecting contaminants also enables optimal operating conditions for mobile & stationary compressors, even in challenging conditions. In turn, this reduces energy consumption and the associated costs by preventing inefficiencies in the filtration process. This is especially important for industries and organisations looking to reduce their overall energy emissions.
In addition, regularly replacing the filter can further improve efficiency. Replacing the filter at regular intervals prevents damage and clogging. When filters become clogged, the system and machinery must work harder. By ensuring filters are changed before they exceed capacity, the associated workload is reduced, and less energy is required to operate equipment.
Furthermore, the clean air supplied by vacuum compressor filters ensures consistent performance and operation, consequently reducing downtime and the risk of disruption. This helps maintain product quality and prevents contamination.
Applications of Vacuum Compressor Filters
Vacuum compressor filters have several applications across various industries, where the cleanliness and purity of compressed air and gas are essential to business operations.
Manufacturing
By filtering out impurities and contaminants, air filters are used to ensure product quality and integrity in manufacturing. Vacuum compressor filters purify the air in machinery and product lines to prevent defects and maintain a consistent standard.
Food and Beverage
In the food and beverage industry, vacuum filters and the filtration process are often used to separate particulates from beverages and extract compounds from food samples. This plays a crucial role in allowing food and beverage production companies to maintain hygiene and safety standards. Typically, air filters are also used to control and remove contaminants from compressed air used in food processing, packaging, and storage.
Pharmaceuticals
In pharmaceuticals, vacuum compressor filters are essential to pharmaceutical manufacturing processes. They help to efficiently separate and collect solid compounds from a sample mixture. This method ensures the purity and quality of the final compound.
Automotive
Air filters are used in various automotive industry applications, including paint booths, assembly lines, and tools. By utilising vacuum compressor filters, automotive businesses can rely on quality paintwork and finishes, production efficiency, and high performance.
Different types of vacuum compressor filters
There are also several different types of vacuum compressor filters. To determine which vacuum filter you need, consider the operating conditions, identify the contaminants, and evaluate the installation requirements.
Some types of vacuum compressor filters include:
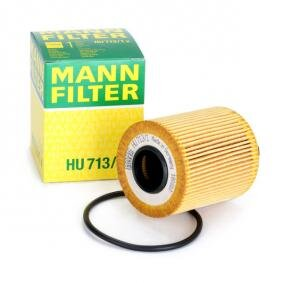
Oil Filter
Oil filters are indispensable components in vacuum compressor systems, providing essential protection against contaminants that could jeopardise the efficiency and longevity of the equipment. They excel in capturing particles of various sizes suspended in the lubricating oil. This includes contaminants like dust, dirt, metal particles, and other debris that can accumulate during operation. By efficiently trapping these particles, oil filters prevent them from circulating through the compressor system and causing damage to critical components.
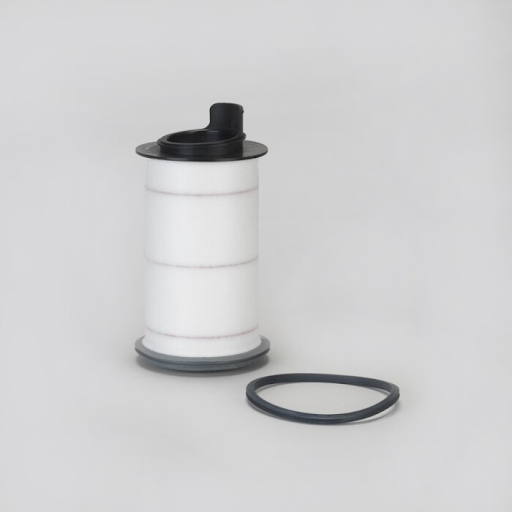
Air/Oil Separators
Air/oil separators are critical for maintaining the purity of compressed air and preventing oil contamination in vacuum compressor systems. They are designed to capture oil droplets from the air stream as it passes through. Coalescing filters use fine fibres to trap oil droplets, while centrifugal elements utilise centrifugal force to separate oil from the air. Their efficient oil separation capability helps to prolong the life of downstream equipment and ensures reliable operation of the entire system.
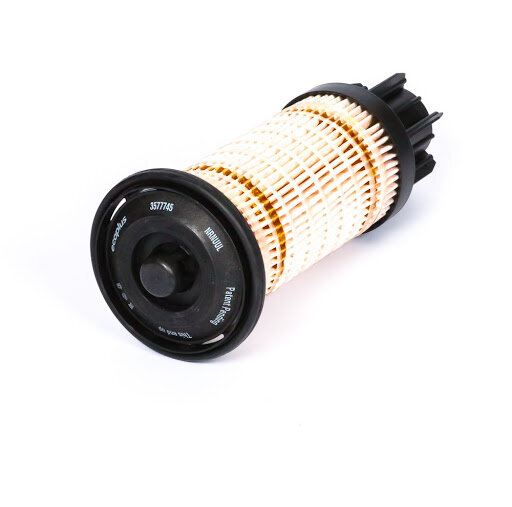
Fuel Filter
Fuel filters are designed to remove contaminants present in the fuel supply, including dirt, rust, debris, and other particulate matter. These contaminants can enter the fuel system during storage, transportation, or handling, posing a risk of clogging fuel lines, injectors, and other critical components. By effectively trapping contaminants, fuel filters prevent them from reaching sensitive parts of the compressor system, ensuring uninterrupted operation and preventing potential damage.
Factors Influencing Filter Efficiency
Several factors can influence the efficiency of vacuum compressor filters. Understanding these factors can help you choose the right filter and optimise filter performance to improve efficiency.
Type of contaminants
The nature and size of contaminants can significantly impact filter performance and efficiency. Filters are designed to capture specific types of particles. Therefore, it is crucial to match the filter type to the contaminant.
Filtration media
The material of the filtration media determines the filter's efficiency. Different filtration media have varying pore sizes and surface properties that impact their ability to capture contaminants. Refer to the manufacturer recommendations for suitable filtration media.
Airflow rate
High airflow rates can reduce efficiency during the filtration process if the filter media cannot capture contaminants at high velocity. Therefore, it is essential to choose a vacuum filter that can maintain high efficiency at the required airflow rate.
Installation and sealing
Proper installation and sealing are essential to maximising efficiency. Poorly installed filters or leaks in the system can allow contaminants to bypass the filter. Always ensure the seal is tight to ensure efficient filtration.
Filter maintenance
For maximum efficiency, regular maintenance, such as inspection, cleaning, and filter replacement, is required. If a filter is clogged, it can cause pressure to drop, reducing airflow and efficiency.
Filtration Vacuum Compressor Filters
We provide Vacuum Compressor filters designed to deliver superior performance and reliability in demanding environments. Whether it's air, oil, or fuel filtration, we can provide parts that effectively remove contaminants while maintaining optimal flow rates and pressure levels. This ensures the continued efficiency and longevity of vacuum compressor systems, even under tough operating conditions.
At Filtration, we are experts in filtration technology and a leading supplier of quality filtration products to a wide range of industries across the UK. We provide a variety of vacuum compressor filters, alongside additional services such as cataloguing, consignment stock, bespoke labelling, oil analysis, and LEV testing.
No matter what you need, Filtration has the solution to meet your filtration needs and will support you every step of the way.
Get in touch today to discover how we can help improve your filtration processes and keep your operations running smoothly.